Сопротивление скольжению по сухой и влажной поверхности
Предлагаю сперва прочитать статью под заголовком "Сопротивление скольжению по сухой и влажной поверхности", которая представлена на сайте. В этой объёмной статье говорится о коэффициенте трения (динамическом и статическом), методах испытания плитки на определение степени скольжения, указаны соответствующие стандарты. Полагаю это будет подробным ответом.
В вашем примере кирпичное основание размещено прямо на грунт. Также видно, что кирпич пористый имеет значительное водопоглощение. Благодаря этому влага из грунта может спокойно проникать в кирпичное основание, а под действием сезонных факторов (особенно температурных колебаний) происходят изменения, которые мы отчётливо наблюдаем на покрытии. Удивляться и расстраиваться не стоит, поскольку в этом случае такой процесс неизбежен. Далее приведу два решения на заданные вопросы.
Решение 1 – кардинальное. Разобрать кирпичное основание полностью, залить фундамент или столбы из бетона, сделать гидроизоляцию, установить основание лестницы, выполнить облицовку плиткой, установить козырёк над крыльцом. Такой подход позволит сохранить покрытие крыльца на десятилетия.
Решение 2 – простое. Провести реставрацию существующего крыльца материалами начального ценового сегмента. Далее по мере необходимости, примерно раз в 2-3 года, производить реставрацию покрытия и основания.
Большинство глазурованных и неглазурованных керамических плиток и плит имеют незначительное естественное влажностное расширение, которое можно не учитывать, что при соблюдении технологии укладки плиток и плит не вызывает проблем.
Однако при нарушении технологии укладки, а также в определенных климатических условиях влажностное расширение может вызвать проблемы, прежде всего там, где укладка керамических плиток и плит производится на бетон, не достигший необходимого возраста. В этих случаях верхний предел влажностного расширения керамических плиток и плит рекомендовано принимать 0,06 %, если применяется испытание согласно стандарту ISO 10545-10.
В конце статьи идёт речь об неэмалированной (неглазурованной) плитке группы I. Согласно стандарта EN 14411 в эту группу входят экструзионные керамические плитки и керамические плитки полусухого прессования с водопоглощением меньшим или равным 3 %.
Морозостойкость - способность керамической плитки многократно выдерживать замораживание во влажной среде при температурах ниже ноля градусов Цельсия. Замерзание неморозостойкой керамической плитки может привести к образованию разрывов и к обламыванию плитки. При использовании керамической плитки замечена следующая закономерность: чем ниже водопоглощение, тем больше вероятность, что материал морозоустойчив. Однако, существуют высокопористые керамические материалы, характеризующиеся высокой степенью морозостойкости. Например, кирпичи, водопоглощение которых составляет 10-15 %. Морозостойкая плитка необходима для облицовки поверхностей, которые подвергаются воздействиям влажной среды и низких температур.
Более подробно материал на эту тему представлен в статье Морозостойкость.
Предлагаю сперва прочитать статью под заголовком "Устойчивость к истиранию, износостойкость", которая представлена на сайте. В этой небольшой статье говорится о способах испытания на устойчивость к истиранию неглазурованной и глазурованной плитки, указаны соответствующие стандарты. Для глазурованной плитки приведены классы износостойкости. Полагаю это будет подробным ответом.
Спасибо, информация в статье изложена подробно и доступно. Ранее я её не видела. Получилось, что я задала вопрос, а это привело к появлению статьи на сайте, приятно.
Как было указано в статье, добавление оксидов металлов позволяет получать цветные глазури. Из практики известно как влияют такие компоненты на получаемый цвет. Итак:
оксид железа - коричневый цвет;
оксид кобальта - синий цвет;
оксид хрома - зелёный цвет;
оксид меди - светло-зелёный, чёрный, красный цвет;
Сырьём для магнезиальных вяжущих служат магнезит и доломит. Обжиг магнезита производится при температуре 750 ... 800°С (во вращающихся печах до 1000°С) до полного разложения MgСО3 на MgO и СО2 с удалением углекислого газа. После помола MgO представляет собой воздушное вяжущее вещество, называемое каустическим магнезитом, оно имеет предел прочности при сжатии 40 ... 60 МПа, достигая иногда до 100 МПа.
Обжиг доломита производят при более низких температурах в интервале 650 ... 750°С, так как при повышении температуры обжига начинает разлагаться и СаСО3 с образованием извести. Особенностью применения магнезиальных вяжущих веществ является затворение их водными растворами магнезиальных солей, причём начало схватывания наступает не позднее 20 мин, а конец — не позднее 6 ч. Магнезиальные вяжущие вещества имеют хорошее сцепление с органическими заполнителями и применяются для производства либо с древесными опилками — ксилолита, либо с древесной шерстью (узкой и длинной древесной стружкой) — фибролита. Ксилолит используется для изготовления бесшовных полов и облицовочной плитки, фибролит — для производства теплоизоляционных изделий и перегородок помещений в поселковом строительстве.
Сырьё для производства воздушной извести служат плотные известняки, ракушечники, мел, доломитизированные известняки при условии, что содержание глинистых примесей в них не превышает 6%. Сырьё обжигают при температуре 1000 ... 1200°С до полного удаления углекислого газа. После обжига получают комовую известь или известь-кипелку (так её называют из-за бурной химической реакции с водой). Это вещество обладает сильно развитой внутренней микропористостью и большим запасом свободной внутренней энергии, что проявляется при гашении комовой извести, т. е. присоединении воды с выделением большого количества теплоты. Известняки при обжиге разлагаются на известь СаО и углекислый газ, который полностью удаляется. Реакция разложения известняка обратимая.
Признаком высокого качества извести является высокое содержание в ней СаО + MgO. Недожог и пережог извести в печи снижают её качество. Особенно опасен пережог — остеклованная известь. Частицы пережога медленно гасятся с увеличением в объёме и могут вызвать трещины в штукатурке и изделиях. Содержание чистых окислов CaO + MgO в общем количестве извести называют её активностью. По активности и содержанию непогасившихся зёрен определяется сорт извести. Если комовую известь измельчить, то получится молотая негашёная. Более распространена в строительстве известь гашёная, получаемая путём затворения водой негашёной извести. При выделении теплоты часть воды гашения превращается в пар, под воздействием которого комовая известь превращается в тончайшие частицы гидратной извести размером в несколько микрон с высокой удельной поверхностью. Гашёная известь медленно схватывается и твердеет, обладает низкой прочностью, поэтому кроме гашеной извести в строительстве применяют известь негашеную. По содержанию оксида магния в извести она подразделяется на кальциевую (MgO < 5%), магнезиальную (MgO = 5 ... 20%) и доломитовую (MgO = 20 ... 40%); по времени гашения различают известь быстрогасящуюся (время гашения < 8 мин), среднегасящуюся (время гашения 8 ... 25 мин) и медленногасящуюся (время гашения не менее 25 мин).
Воздушную известь применяют для приготовления кладочных и отделочных растворов, изготовления штучных бетонных изделий, например известковошлаковых, силикатного кирпича и других известково-песчаных изделий автоклавного твердения.
Для начала следует ознакомиться с определениями следующих терминов: гипс, ангидрит. В зависимости от способа получения гипсовые вяжущие вещества делятся на три основные группы:
вяжущие, получаемые термической обработкой гипсового сырья: низкообжиговые (обжиговые и варочные) и высокообжиговые;
вяжущие, получаемые без термической обработки (безобжиговые);
вяжущие, получаемые смешиванием гипсовых вяжущих I или II групп с различными компонентами (минеральными и химическими).
В I группу входят: гипсовые вяжущие, основной составляющей которых является α- или β-полугидрат сульфата кальция (или их смесь), а также растворимый ангидрит; ангидритовые вяжущие, состоящие, главным образом, из полностью обезвоженного гипса или даже частично диссоциированного ангидрита, содержащего небольшое количество свободного оксида кальция.
Во II группу входят: вяжущие, получаемые на основе природного двугидрата сульфата кальция; вяжущие, получаемые на основе природного ангидрита. Для активации твердения этих вяжущих вводятся специальные добавки.
В III группу входят вяжущие, получаемые смешиванием гипсовых вяжущих I и II групп с различными компонентами (известь, портландцемент и его разновидности, активные минеральные добавки, химические добавки и др.).
Вяжущие I и II групп являются неводостойкими (воздушными) гипсовыми вяжущими. Вяжущие III группы относятся, за некоторым исключением, к водостойким гипсовым вяжущим.
Основными характеристиками гипсовых вяжущих являются: цвет, плотность, удельная поверхность, тонкость помола; водопотребность; сроки схватывания теста; механическая прочность, старение и др.
Цвет гипсовых вяжущих зависит от химической чистоты гипсового сырья, содержания примесей и способа производства. Гипсовые вяжущие белого цвета получают из чистого сырья, а серого - из сырья с примесями минерального и органического происхождения. Плотность определяют по ГОСТ 6427. Значения истинной, насыпной в уплотненном и насыпной в рыхлом состоянии плотности гипсовых вяжущих составляют соответственно 2,6–2,75 г/см3, 1200–1450 и 800–1100 кг/м3. Внешняя удельная поверхность гипсовых вяжущих веществ - это суммарная поверхность всех зерен в единице объема или массы - находится в пределах 0,3–0,5 м2/г, а высокопрочных - 0,09–0,12 м2/г. Тонкость помола характеризует степень измельчения гипсового вяжущего и выражается остатком в массовых процентах на стандартном сите № 02, либо удельной поверхностью порошка вяжущего в м2/кг (см2/г). Водопотребность является важнейшим свойством гипсовых вяжущих и характеризует минимальное количество воды, необходимое для получения теста заданной консистенции. Отношение количества воды к массе гипсового вяжущего называется водогипсовым отношением (В/Г). Теоретически для гидратации полугидрата сульфата кальция необходимо 18,62 % воды от массы вяжущего. Практически для получения теста нормальной густоты из β-полугидрата сульфата кальция требуется 50–70 %, для α-полугидрата сульфата кальция – 30–40%, для ангидритовых вяжущих – 30–35 %. Водостойкие гипсовые вяжущие в зависимости от состава и технологии получения могут иметь нормальную густоту от 30 до 65 %. Вода, остающаяся в гипсовом камне после гидратации испаряется, образуя в нем поры и капилляры, отрицательно влияющие на физико-технические свойства вяжущих. Механическая прочность затвердевшего гипсового вяжущего определяется по результатам испытаний стандартных образцов на изгиб и (или) сжатие после твердения. При стандартных режимах твердения прочность высушенных образцов становится в 2 и более раз выше прочности образцов через 2 ч после формования. Так прочность образцов из строительного гипса через 2 ч составляет 4–6 МПа, а сухих 10–16 МПа, из формовочного гипса соответственно – 6–8 и 18–20 МПа, из высокопрочного – 15–20 и 35–40, супергипса – 22–30 и 60–70 МПа.
Согласно ГОСТ 31189 по применяемым вяжущим сухие смеси подразделяют на:
цементные;
гипсовые;
известковые;
магнезиальные;
полимерные;
композиционные.
А в эпоксидных клеях или затирках как это работает? Там какое вяжущее? В смысле, я знаю что там два компонента и при смешивании они твердеют, но что там происходит, так сказать, на молекулярном уровне? Что во что заходит и кто кого вяжет :)))))))
Постепенно доберёмся и до эпоксидных клеёв и затирок. Пока только цементные слегка охватили.
А в эпоксидных клеях или затирках как это работает? Там какое вяжущее? В смысле, я знаю что там два компонента и при смешивании они твердеют, но что там происходит, так сказать, на молекулярном уровне? Что во что заходит и кто кого вяжет :)))))))
Портландцемент часто называется просто цементом – это важнейшее минеральное вяжущее вещество. Он служит базовым материалом для большинства модифицированных специальных цементов, в то же время он может и без модификации применяться в широком диапазоне условий цементирования. Портландцемент – порошкообразный материал, содержащий искусственные минералы, большинство которых в природе не встречаются или встречаются крайне редко. Эти минералы обладают высокой химической активностью и способны взаимодействовать с водой.
Портландцементом называется гидравлическое вяжущее вещество, получаемое тонким измельчением портландцементного клинкера с гипсом и другими специальными добавками. Клинкер получают обжигом до спекания тонкодисперсной однородной сырьевой смеси, состоящей из известняка, глины, кремнезёма. Гипс вводится с целью регулирования, скорости схватывания и некоторых других свойств. Клинкерный порошок без гипса при смешивании с водой быстро схватывается и затвердевает в цементный камень с пониженными прочностными свойствами. Согласно ГОСТ 1581-96 в портландцемент разрешается вводить при помоле до 15 % активных минеральных добавок. При этом, название, цемента не меняется. Свойства портландцемента определяются, прежде всего, качеством клинкера.
Историческая справка. Считается, что портландцемент был изобретён в Англии каменщиком Джозефом Аспдином, который получил патент в 1824 г. на изготовление вяжущего вещества из смеси извести с глиной обжигом её до полного удаления углекислоты. Это вяжущее он назвал портландцементом. Однако в России, портландцемент был получен несколько ранее, в 1817 г. начальником военно-рабочей команды Е. Г. Челиевым. В 1825 г. им была издана книга о получении вяжущего вещества, аналогичного по составу применяемому ныне портландцементу.
В общем случае, минеральными вяжущими веществами называются тонкодисперсные порошки моно- или полиминерального состава, которые при затворении водой или растворами солей способны образовывать коагуляционные и кристаллизационные структуры, обладающие определенной прочностью и долговечностью. По способности вяжущих веществ образовывать структуру они делятся на три группы:
Воздушные вяжущие вещества - это вещества, способные твердеть и длительно сохранять свою прочность только на воздухе. К этой группе относятся гипсовые, известковые, магнезиальные вяжущие вещества и кислотоупорный цемент;
Гидравлические вяжущие вещества - это вещества, способные твердеть и длительно сохранять свою прочность, как на воздухе, так и в воде. К этой группе относятся портландцемент и его разновидности, цементы на шлаковой основе, глиноземистые цементы и др.;
Вяжущие гидротермального твердения - это вещества, способные образовывать искусственный камень только в гидротермальных условиях (при высоких температурах и давлении). К этому типу относятся известково-кремнеземистые, белито-кремнеземистые, шлакопесчаные составы и др.
Все рассмотренные вяжущие относятся к вяжущим гидратационного твердения, т.е. для получения твердого камня из них требуется затворение вяжущего водой, только в первом случае твердение происходит на воздухе, во втором в воде, в третьем – в воде при температуре и давлении.
Через 100 циклов замораживания/оттаивания проводят исследование лицевых поверхностей и граней керамических плиток или плит. Исследование проводится невооруженным глазом или в очках при их постоянном ношении на расстоянии от 25 до 30 см при интенсивности освещения 300 лк. Для ускорения предоставления отчета при выявлении относительно раннего наступления повреждений допускается их выборочная проверка. Все повреждения, выявленные на лицевой поверхности и на гранях керамических плиток или плит, регистрируют.
Предлагаю сперва прочитать статью под заголовком "Сопротивление скольжению по сухой и влажной поверхности", которая представлена на сайте. В этой объёмной статье говорится о коэффициенте трения (динамическом и статическом), методах испытания плитки на определение степени скольжения, указаны соответствующие стандарты. Полагаю это будет подробным ответом.
Могли бы пояснить, что это за группы и как их использовать?
В вашем примере кирпичное основание размещено прямо на грунт. Также видно, что кирпич пористый имеет значительное водопоглощение. Благодаря этому влага из грунта может спокойно проникать в кирпичное основание, а под действием сезонных факторов (особенно температурных колебаний) происходят изменения, которые мы отчётливо наблюдаем на покрытии. Удивляться и расстраиваться не стоит, поскольку в этом случае такой процесс неизбежен. Далее приведу два решения на заданные вопросы.
Решение 1 – кардинальное. Разобрать кирпичное основание полностью, залить фундамент или столбы из бетона, сделать гидроизоляцию, установить основание лестницы, выполнить облицовку плиткой, установить козырёк над крыльцом. Такой подход позволит сохранить покрытие крыльца на десятилетия.
Решение 2 – простое. Провести реставрацию существующего крыльца материалами начального ценового сегмента. Далее по мере необходимости, примерно раз в 2-3 года, производить реставрацию покрытия и основания.
Влажностное расширение керамической плитки
Большинство глазурованных и неглазурованных керамических плиток и плит имеют незначительное естественное влажностное расширение, которое можно не учитывать, что при соблюдении технологии укладки плиток и плит не вызывает проблем.
Однако при нарушении технологии укладки, а также в определенных климатических условиях влажностное расширение может вызвать проблемы, прежде всего там, где укладка керамических плиток и плит производится на бетон, не достигший необходимого возраста. В этих случаях верхний предел влажностного расширения керамических плиток и плит рекомендовано принимать 0,06 %, если применяется испытание согласно стандарту ISO 10545-10.
При выборе керамической плитки важным критерием является сопротивление скольжению по сухой (группы R9 - R13) и влажной (группы A, B, C) поверхности.
Неэмалированная плитка Группы I
В конце статьи идёт речь об неэмалированной (неглазурованной) плитке группы I. Согласно стандарта EN 14411 в эту группу входят экструзионные керамические плитки и керамические плитки полусухого прессования с водопоглощением меньшим или равным 3 %.
Морозостойкость - способность керамической плитки многократно выдерживать замораживание во влажной среде при температурах ниже ноля градусов Цельсия. Замерзание неморозостойкой керамической плитки может привести к образованию разрывов и к обламыванию плитки. При использовании керамической плитки замечена следующая закономерность: чем ниже водопоглощение, тем больше вероятность, что материал морозоустойчив. Однако, существуют высокопористые керамические материалы, характеризующиеся высокой степенью морозостойкости. Например, кирпичи, водопоглощение которых составляет 10-15 %. Морозостойкая плитка необходима для облицовки поверхностей, которые подвергаются воздействиям влажной среды и низких температур.
Более подробно материал на эту тему представлен в статье Морозостойкость.
Спасибо, информация в статье изложена подробно и доступно. Ранее я её не видела. Получилось, что я задала вопрос, а это привело к появлению статьи на сайте, приятно.
Приведу чертежи из рекомендаций по укладки ступеней немецкого производителя керамических ступеней Interbau blink:
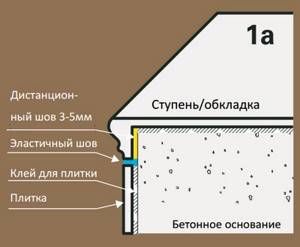
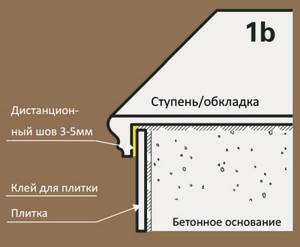
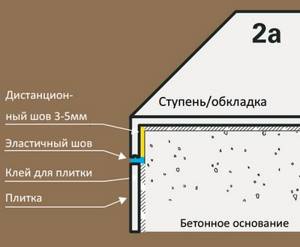
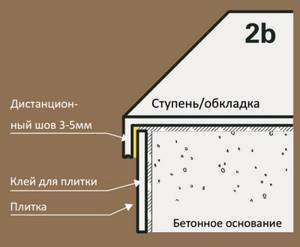
Видно, что можно использовать оба варианта. Желающие могут ознакомиться с инструкцией полностью по ссылке.
Оксиды металлов
Как было указано в статье, добавление оксидов металлов позволяет получать цветные глазури. Из практики известно как влияют такие компоненты на получаемый цвет. Итак:
Сырьём для магнезиальных вяжущих служат магнезит и доломит. Обжиг магнезита производится при температуре 750 ... 800°С (во вращающихся печах до 1000°С) до полного разложения MgСО3 на MgO и СО2 с удалением углекислого газа. После помола MgO представляет собой воздушное вяжущее вещество, называемое каустическим магнезитом, оно имеет предел прочности при сжатии 40 ... 60 МПа, достигая иногда до 100 МПа.
Обжиг доломита производят при более низких температурах в интервале 650 ... 750°С, так как при повышении температуры обжига начинает разлагаться и СаСО3 с образованием извести. Особенностью применения магнезиальных вяжущих веществ является затворение их водными растворами магнезиальных солей, причём начало схватывания наступает не позднее 20 мин, а конец — не позднее 6 ч. Магнезиальные вяжущие вещества имеют хорошее сцепление с органическими заполнителями и применяются для производства либо с древесными опилками — ксилолита, либо с древесной шерстью (узкой и длинной древесной стружкой) — фибролита. Ксилолит используется для изготовления бесшовных полов и облицовочной плитки, фибролит — для производства теплоизоляционных изделий и перегородок помещений в поселковом строительстве.
Сырьё для производства воздушной извести служат плотные известняки, ракушечники, мел, доломитизированные известняки при условии, что содержание глинистых примесей в них не превышает 6%. Сырьё обжигают при температуре 1000 ... 1200°С до полного удаления углекислого газа. После обжига получают комовую известь или известь-кипелку (так её называют из-за бурной химической реакции с водой). Это вещество обладает сильно развитой внутренней микропористостью и большим запасом свободной внутренней энергии, что проявляется при гашении комовой извести, т. е. присоединении воды с выделением большого количества теплоты. Известняки при обжиге разлагаются на известь СаО и углекислый газ, который полностью удаляется. Реакция разложения известняка обратимая.
Признаком высокого качества извести является высокое содержание в ней СаО + MgO. Недожог и пережог извести в печи снижают её качество. Особенно опасен пережог — остеклованная известь. Частицы пережога медленно гасятся с увеличением в объёме и могут вызвать трещины в штукатурке и изделиях. Содержание чистых окислов CaO + MgO в общем количестве извести называют её активностью. По активности и содержанию непогасившихся зёрен определяется сорт извести. Если комовую известь измельчить, то получится молотая негашёная. Более распространена в строительстве известь гашёная, получаемая путём затворения водой негашёной извести. При выделении теплоты часть воды гашения превращается в пар, под воздействием которого комовая известь превращается в тончайшие частицы гидратной извести размером в несколько микрон с высокой удельной поверхностью. Гашёная известь медленно схватывается и твердеет, обладает низкой прочностью, поэтому кроме гашеной извести в строительстве применяют известь негашеную. По содержанию оксида магния в извести она подразделяется на кальциевую (MgO < 5%), магнезиальную (MgO = 5 ... 20%) и доломитовую (MgO = 20 ... 40%); по времени гашения различают известь быстрогасящуюся (время гашения < 8 мин), среднегасящуюся (время гашения 8 ... 25 мин) и медленногасящуюся (время гашения не менее 25 мин).
Воздушную известь применяют для приготовления кладочных и отделочных растворов, изготовления штучных бетонных изделий, например известковошлаковых, силикатного кирпича и других известково-песчаных изделий автоклавного твердения.
Для начала следует ознакомиться с определениями следующих терминов: гипс, ангидрит. В зависимости от способа получения гипсовые вяжущие вещества делятся на три основные группы:
В I группу входят: гипсовые вяжущие, основной составляющей которых является α- или β-полугидрат сульфата кальция (или их смесь), а также растворимый ангидрит; ангидритовые вяжущие, состоящие, главным образом, из полностью обезвоженного гипса или даже частично диссоциированного ангидрита, содержащего небольшое количество свободного оксида кальция.
Во II группу входят: вяжущие, получаемые на основе природного двугидрата сульфата кальция; вяжущие, получаемые на основе природного ангидрита. Для активации твердения этих вяжущих вводятся специальные добавки.
В III группу входят вяжущие, получаемые смешиванием гипсовых вяжущих I и II групп с различными компонентами (известь, портландцемент и его разновидности, активные минеральные добавки, химические добавки и др.).
Вяжущие I и II групп являются неводостойкими (воздушными) гипсовыми вяжущими. Вяжущие III группы относятся, за некоторым исключением, к водостойким гипсовым вяжущим.
Основными характеристиками гипсовых вяжущих являются: цвет, плотность, удельная поверхность, тонкость помола; водопотребность; сроки схватывания теста; механическая прочность, старение и др.
Цвет гипсовых вяжущих зависит от химической чистоты гипсового сырья, содержания примесей и способа производства. Гипсовые вяжущие белого цвета получают из чистого сырья, а серого - из сырья с примесями минерального и органического происхождения.
Плотность определяют по ГОСТ 6427. Значения истинной, насыпной в уплотненном и насыпной в рыхлом состоянии плотности гипсовых вяжущих составляют соответственно 2,6–2,75 г/см3, 1200–1450 и 800–1100 кг/м3.
Внешняя удельная поверхность гипсовых вяжущих веществ - это суммарная поверхность всех зерен в единице объема или массы - находится в пределах 0,3–0,5 м2/г, а высокопрочных - 0,09–0,12 м2/г.
Тонкость помола характеризует степень измельчения гипсового вяжущего и выражается остатком в массовых процентах на стандартном сите № 02, либо удельной поверхностью порошка вяжущего в м2/кг (см2/г).
Водопотребность является важнейшим свойством гипсовых вяжущих и характеризует минимальное количество воды, необходимое для получения теста заданной консистенции. Отношение количества воды к массе гипсового вяжущего называется водогипсовым отношением (В/Г). Теоретически для гидратации полугидрата сульфата кальция необходимо 18,62 % воды от массы вяжущего. Практически для получения теста нормальной густоты из β-полугидрата сульфата кальция требуется 50–70 %, для α-полугидрата сульфата кальция – 30–40%, для ангидритовых вяжущих – 30–35 %. Водостойкие гипсовые вяжущие в зависимости от состава и технологии получения могут иметь нормальную густоту от 30 до 65 %. Вода, остающаяся в гипсовом камне после гидратации испаряется, образуя в нем поры и капилляры, отрицательно влияющие на физико-технические свойства вяжущих.
Механическая прочность затвердевшего гипсового вяжущего определяется по результатам испытаний стандартных образцов на изгиб и (или) сжатие после твердения. При стандартных режимах твердения прочность высушенных образцов становится в 2 и более раз выше прочности образцов через 2 ч после формования. Так прочность образцов из строительного гипса через 2 ч составляет 4–6 МПа, а сухих 10–16 МПа, из формовочного гипса соответственно – 6–8 и 18–20 МПа, из высокопрочного – 15–20 и 35–40, супергипса – 22–30 и 60–70 МПа.
Согласно ГОСТ 31189 по применяемым вяжущим сухие смеси подразделяют на:
Постепенно доберёмся и до эпоксидных клеёв и затирок. Пока только цементные слегка охватили.
Всю жизнь думал, что портландцемент назван в честь города Портленд :)))))) Спасибо за историческую справку!
А в эпоксидных клеях или затирках как это работает? Там какое вяжущее? В смысле, я знаю что там два компонента и при смешивании они твердеют, но что там происходит, так сказать, на молекулярном уровне? Что во что заходит и кто кого вяжет :)))))))
Портландцемент часто называется просто цементом – это важнейшее минеральное вяжущее вещество. Он служит базовым материалом для большинства модифицированных специальных цементов, в то же время он может и без модификации применяться в широком диапазоне условий цементирования. Портландцемент – порошкообразный материал, содержащий искусственные минералы, большинство которых в природе не встречаются или встречаются крайне редко. Эти минералы обладают высокой химической активностью и способны взаимодействовать с водой.
Портландцементом называется гидравлическое вяжущее вещество, получаемое тонким измельчением портландцементного клинкера с гипсом и другими специальными добавками. Клинкер получают обжигом до спекания тонкодисперсной однородной сырьевой смеси, состоящей из известняка, глины, кремнезёма. Гипс вводится с целью регулирования, скорости схватывания и некоторых других свойств. Клинкерный порошок без гипса при смешивании с водой быстро схватывается и затвердевает в цементный камень с пониженными прочностными свойствами. Согласно ГОСТ 1581-96 в портландцемент разрешается вводить при помоле до 15 % активных минеральных добавок. При этом, название, цемента не меняется. Свойства портландцемента определяются, прежде всего, качеством клинкера.
Историческая справка. Считается, что портландцемент был изобретён в Англии каменщиком Джозефом Аспдином, который получил патент в 1824 г. на изготовление вяжущего вещества из смеси извести с глиной обжигом её до полного удаления углекислоты. Это вяжущее он назвал портландцементом. Однако в России, портландцемент был получен несколько ранее, в 1817 г. начальником военно-рабочей команды Е. Г. Челиевым. В 1825 г. им была издана книга о получении вяжущего вещества, аналогичного по составу применяемому ныне портландцементу.
В общем случае, минеральными вяжущими веществами называются тонкодисперсные порошки моно- или полиминерального состава, которые при затворении водой или растворами солей способны образовывать коагуляционные и кристаллизационные структуры, обладающие определенной прочностью и долговечностью. По способности вяжущих веществ образовывать структуру они делятся на три группы:
Все рассмотренные вяжущие относятся к вяжущим гидратационного твердения, т.е. для получения твердого камня из них требуется затворение вяжущего водой, только в первом случае твердение происходит на воздухе, во втором в воде, в третьем – в воде при температуре и давлении.
Выявление повреждений лицевых поверхностей и граней
Через 100 циклов замораживания/оттаивания проводят исследование лицевых поверхностей и граней керамических плиток или плит. Исследование проводится невооруженным глазом или в очках при их постоянном ношении на расстоянии от 25 до 30 см при интенсивности освещения 300 лк. Для ускорения предоставления отчета при выявлении относительно раннего наступления повреждений допускается их выборочная проверка. Все повреждения, выявленные на лицевой поверхности и на гранях керамических плиток или плит, регистрируют.
Классификация керамических плиток и плит по водопоглощению
По водопоглощению керамические плитки и плиты подразделяются на следующие три группы:
В группе I есть дополнительное разделение: E < 0,5 %; 0,5 % < E < 3 %.
В группе II есть дополнительное разделение 3 % < E < 6 %; 6 % < E < 10 %.
Страницы